Introduction
Every product we use or see has a price tag (cost + margin), that pricing decision can be the difference between a product being successful or flop. In traditional costing the variable costs are spread across the products line uniformly irrespective of the product consuming that cost or not. However different products require different tools, skills, and time duration (labor hours) to produce. While the fixed costs remain the same, the overhead costs vary, which in turn makes the total cost different for each product produced under the same facility line. The focus of the activity-based costing method is on those activities which increase the variable/overhead cost of the product. It is a more sophisticated method of cost allocation than the traditional volume-based costing method.
The activity based costing or ABC first introduced by Kaplan and Cooper in the 1980s. This model focuses on the indirect costs of production, in contrast to the absorption cost allocation method of traditional costing.
Definition of Activity Based Costing
Activity Based Costing is an approach that an organization needs to identify factors or resources that contribute to the occurrence of costs of that organization’s major activities. That means all support overhead costs shall be charged to each product based on their usage of factors causing such overheads.
Similarly, the Chartered Institute of Management Accountants defines ABC as:
“An approach to the costing and monitoring of the activities which involves tracing resource consumption and costing final outputs. Resources are assigned to activities, and activities to cost objects based on consumption estimates. The latter utilizes cost drivers to attach activity costs to output.” CIMA Offical
So how does the ABC differ from the traditional costing method? In traditional costing; the overhead costs are also absorbed based on the fixed costs to get the total cost per unit. This is known as Absorption Costing. An increased volume of production and a variety of products in the same production facility means the overhead costs may differ significantly for different products affecting the pricing decision.
The ABC method for example takes into consideration the marketing and advertisement costs, which may have different allocated budgets for different brand products. This returns for the different variable costs per unit for the products produced in the same production facility. The same applies to the service industry.
The ABC approach assumes that the products should absorb the costs for the activities which arise as a result of that particular product being produced (or service rendered). These activities sometimes are difficult to identify, the cost is then calculated based on these cost driving activities.
Activity Based Costing Methodology
The cost per unit in the ABC method can be determined using the below four steps approach:
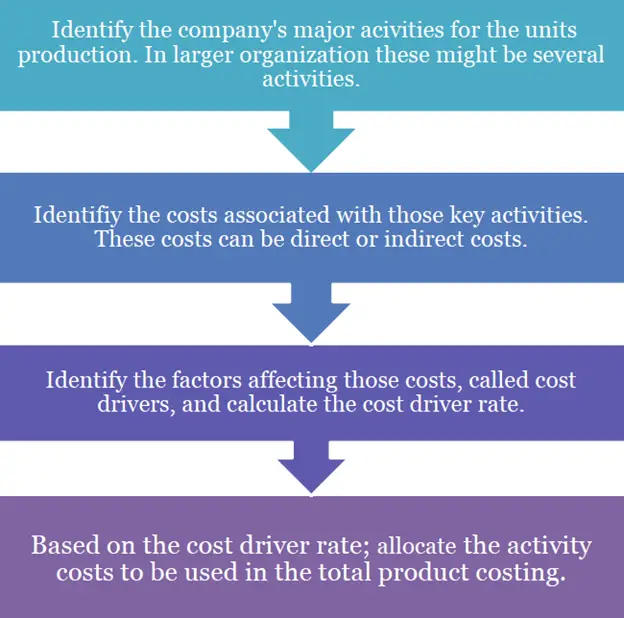
The most significant process in ABC costing is the identification of the critical activities and the cost drivers affecting the output. The reasoning behind the process is that support activities also cause costs; hence those activities should also be allocated a portion of the cost. The factors causing a change in these activities are called cost drivers.
A real-life example will be a manufacturing facility to produce different garment products; where the setup cost for the building will be the same but other costs like maintenance of the machines, direct material, labor hours, and purchase of specific tools will vary with the production of different product lines.
The difference in the overhead costs per unit will vary significantly which will affect the pricing decision and hence the profitability of the product. In the traditional costing method, these overhead costs would be allocated uniformly across all the products (volume-based costing). The activity based costing method first calculates the overhead costs, identifies the cost drivers, and assigns these costs to the products or services rendered. This method has its advantages and disadvantages in comparison to the traditional costing method.
Example of Activity Based Costing
In this section, we will illustrate one example on how to calculate the cost as per the activity-based costing. In addition, we will also provide the comparison how this method defer from the traditional costing.
Example:
Suppose that ABC Co produces four products. These are product P1, P2, P3 and P4. The level outputs and costs are as follow:
Products | Output Units | Number of Production Runs | Material Cost per Unit | Direct Labor Hours per Unit | Machine Hours per Unit |
---|---|---|---|---|---|
P1 | 10 | 3 | 20 | 1 | 1 |
P2 | 10 | 3 | 70 | 2 | 2 |
P3 | 100 | 4 | 20 | 1 | 1 |
P4 | 100 | 4 | 70 | 4 | 4 |
The direct labor hour cost per hour is at US$4.
The data in relation to the manufacturing overhead costs are as follow:
Overheads Costs | US$ |
---|---|
Short-run variable costs | 3,000 |
Set-up costs | 10,500 |
Expediting and scheduling costs | 9,000 |
Materials handling costs | 7,500 |
Total Overheads costs | 30,000 |
Required:
Prepare the unit costs for each product by using the cost method as follow:
(a). Traditional costing – Absorption Costing
(b). Activity-based costing – ABC
Assumption: Assume that in the traditional absorption costing approach, ABC Co uses direct labor hour rate as the overhead absorption rate.
Solution:
(a). Calculate the costs as per the Absorption Costing or traditional costing method.
In the traditional costing, first, we need to calculate the Absorption Overhead Rate or simply Absorption Rate. As per the example above, the adsorption overhead rate is based on the direct labor hours.
Below is the absorption overheads rate formula based on the direct labor hours:
Absorption Overheads Rate = Overhead Costs/Total Direct Labor Hours
Where:
Total Overhead Costs = US$30,000
Total Direct Labor Hours is calculated for the sum of the four products as follow:
P1 = 10*1 = 10 Hours
P2 = 10*2 = 20 Hours
P3 = 100*1 = 100 Hours
P4 = 100*4 = 400 Hours
Thus, the Tota Direct Labor Hours is 530 Hours
Therefore, Absorption Rate = US$30,000 / 530 = US$56.6 per direct labor
The total costs would be summarized as follow:
Products | P1 US$ | P2 US$ | P3 US$ | P4 US$ | TOTAL US$ |
---|---|---|---|---|---|
Direct Material | 200.00 | 700.00 | 2,000.00 | 7,000.00 | 9,900.00 |
Direct Labor | 40.00 | 80.00 | 400.00 | 1,600.00 | 2,120.00 |
Overheads | 566.04 | 1,132.08 | 5,660.38 | 22,641.51 | 30,000.00 |
Total | 806.04 | 1,912.08 | 8,060.38 | 31,241.51 | 42,020.00 |
Units Produced | 10 | 10 | 100 | 100 | |
Cost per Unit | 80.60 | 191.20 | 80.60 | 312.40 |
Note: The calculation of costs of each product is as follow:
- Direct Material:
P1 = 20*10 = US$200
P2 = 70*10 = US$700
P3 = 20*100 = US$2,000
P4 = 70*100 = US$7,000
- Direct Labor:
P1 = 1*4*10 = US$40
P2 = 2*4*10 = US$80
P3 = 1*4*100 = US$400
P4 = 4*4*100 = US$1,600
- Overheads:
P1 = 1*10*56.6 = US$566
P2 = 2*10*56.6 = US$1,132
P3 = 1*100*56.6 = US$5,660
P4 = 4*100*56.6 = US$22,640
(b). Activity-Based Costing Method
Under activity-based costing method, we assume further that the cost driver of set-up costs, expediting and scheduling costs as well as material handling costs is based on the number of production runs. While the cost driver for short-run variable costs is the machine hour.
Thus, the product cost per unit would be as follow:
Products | P1 US$ | P2 US$ | P3 US$ | P4 US$ | TOTAL US$ |
---|---|---|---|---|---|
Direct Material (No change) | 200.00 | 700.00 | 2,000.00 | 7,000.00 | 9,900.00 |
Direct Labor (No change) | 40.00 | 80.00 | 400.00 | 1,600.00 | 2,120.00 |
Short-run variable costs (W1) | 56.60 | 113.21 | 566.04 | 2,264.15 | 3,000.00 |
Set-up costs (W2) | 2,250.00 | 2,250.00 | 3,000.00 | 3,000.00 | 10,500.00 |
Expediting and scheduling costs (W3) | 1,928.57 | 1,928.57 | 2,571.43 | 2,571.43 | 9,000.00 |
Material handling costs (W4) | 1,607.14 | 1,607.14 | 2,142.86 | 2,142.86 | 7,500.00 |
Total | 6,082.32 | 6,678.92 | 10,680.32 | 18,578.44 | 42,020.00 |
Units Produced | 10 | 10 | 100 | 100 | |
Cost per Unit | 608.23 | 667.89 | 106.80 | 185.78 |
Working:
W1: US$3,000 / 530 machine hours = US$5.66 per machine hour
W2: US$10,500 / 14 production runs = US$750 per production run
W3: US$9,000 / 14 production runs = US$642.85 per production run
W4: US$7,500 / 14 production runs = US$535.71 per production run
We can summary the costs for both method as per the table below:
Product | Absorption Costing Unit Cost | ABC Costing Unit Cost | Difference per Unit | Difference in US$ |
---|---|---|---|---|
P1 | 80.60 | 608.23 | +527.63 | +5,276.30 |
P2 | 191.20 | 667.89 | +476.69 | +4,766.90 |
P3 | 80.60 | 106.80 | +26,20 | +2,620.22 |
P4 | 312.40 | 185.78 | -126.62 | -12,662.00 |
From the summary table above, the cost per unit under traditional absorption costing appears to be flawed. This is because the low volume of product P1 and P2 are not allocated with the fair costs of overheads that support the production activities.
However, ABC Costing is able to address these problems. This method is able to arguably produce a more realistic or satisfactory cost by fairly allocating the overheads based the activities consumed.
Advantages of the Activity Based Costing Method
- The ABC method takes into consideration the overhead costs which the traditional costing method ignores hence provides more accurate costing information.
- It considers the cause of the overheads i.e. the cost drivers.
- As it stresses on the key activities and costs related to production, it is also an accurate method of identifying the bottleneck activities for the production units.
- It considers both the financial (cost per activity) as well as non-financial aspects (drivers of the costs), which helps in improved management decisions.
- As this method stresses on cost drivers, it overall increases the monitoring and efficiency of the production facility; a more holistic approach towards competitive operations.
Disadvantages of the Activity Based Costing Method
- As the Activity Based Costing method first identifies the cost drivers, it depends on the historical data which may not be available for new setups.
- It does not help in the rapidly changing
- This method can be applied successfully to the setups where the product range is diverse and the production is in large volume.
- This method is difficult and costly to identify the cost drivers accurately on such a large scale.
- It requires both financial and managerial skills to implement the approach successfully.
Conclusion
Any methodology based on theory cannot guarantee success until implemented in conjunction with other recommended practices. As the ABC method emphasis on accuracy of product costing, it greatly improves strategic decision making in the long term. The ABC method considers historic data from large volume production; it is advised to implement this method for long-run strategy. This method can be more beneficial for organizations where the product line is more diversified; the product line depends on the variable costs more than the fixed costs.