Every product we use is produced in some kind of manufacturing facility. There are different types of costs associated with each unit of product, e.g. Material and labor costs. These costs can be classified into two categories of Fixed and Variable costs. Different costing techniques account for these costs in different ways. Overheads in production can be variable or fixed. The Absorption Costing method takes into account both the fixed and variable overhead costs. As it considers full variable overheads + the fixed costs into consideration it is also called the full costing method.
Definition
“Absorption costing is a principle whereby fixed as well as variable costs are allotted to cost units. Under this system cost per unit is includes fixed expenses in addition to variable costs.” According to CIMA Official
Definition given by CIMA Official
Overhead costs can be both fixed and variable e.g. raw material, skilled labor hour per unit, etc. However, there are indirect overheads that are fixed in nature over the period of production e.g. Electricity costs in a factory, Insurance premium, etc. The absorption costing method argues for the accounting of these both fixed and variable overheads to the units produced whether or not sold by the end of the production period.
The absorption costing theory argues that fixed overhead costs cannot be avoided, so should be included in the inventory costing. For a certain period of production, this increases the ending inventory (unsold items) valuation, decreases the expenses on the income statement, and results in larger profits as all the costs are already accounted for. As the full costing method is used, units produced but unsold in ending inventory do not marginalize the profits.
Calculation Absorption Costing
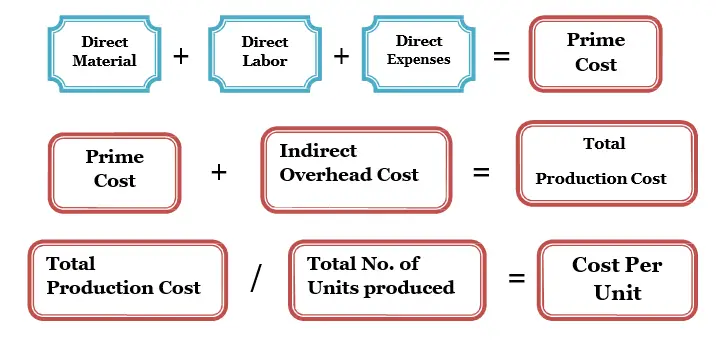
There are three main steps in the absorption costing method:
- Allocation
- Apportion
- Absorption
The allocation of costs refers to the distribution of overhead costs to the relevant departments. A production facility has a manufacturing unit and a service unit. The overhead costs are allocated to the relevant departments.
If the production facility has more than one department e.g. Manufacturing, after-sales service, maintenance, etc then these costs need to be APPORTIONED or shared among these departments. Departments like service centers and marketing are not directly involved in production facilities, so sometimes the apportioned costs do not reflect the true share of that particular department. In that case, the costs are REAPPORTIONED to these departments on a fair basis.
After the allocation and apportioning of the overhead costs, the next step is to absorb those costs. The overhead costs are calculated as per unit costs. There are a number of ways to calculate the absorption costs based on:
- Labor hours per unit
- No. of units produced
- Specific machine hours per unit
- Percent share of the prime cost (direct cost)
Example 1:
Suppose a factory produces wood tables, we’ll calculate the profit under absorption costing method:
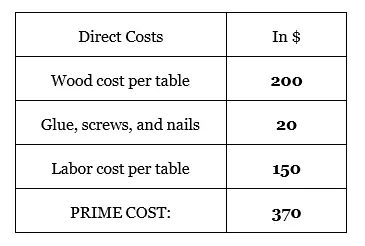
Indirect overhead costs: Total Rent (5000) divided by number of units (50) = 100 Electricity and utilities: Total costs (2000) divided by number of units (50) = 40 Total overhead costs = 140
Total Production cost: 370 + 140 = 510 $ The company decides to sell each table for 700 $. The profit per table= 700 – 510 = 190 $
Total profit over the period: 190 × 50 = 9,500 $
Example 2:
ABC Company is preparing its production overhead budgets and determining to allocate overhead costs to the products. The company has identified the cost centers expenses and related information as follow:
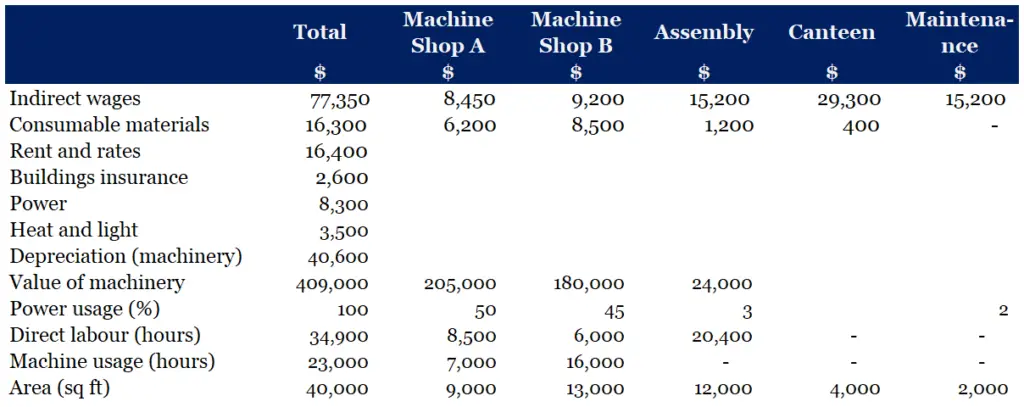
Based on the information above, calculate the production overhead totals for each production department.
From the above information, we can calculate the production overhead cost of each production department as follow:
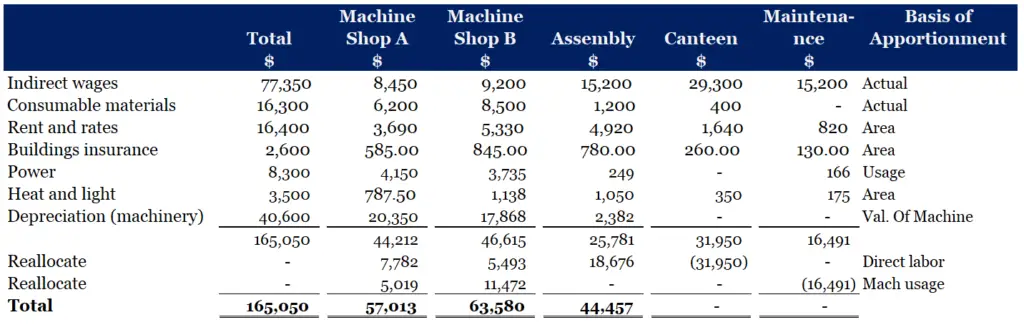
From the above table calculation, to get the total production overhead costs for each production department, the company needs to identify the basis of apportionment and then do the apportion of each overhead cost to each relevant department.
After that, the company shall need to reallocate the overhead costs of the service departments to each production department based on an appropriate basis. In this case, the Canteen department is reallocated based on direct labor while the maintenance department is based on machine usage.
Finally, ABC Company got the total production overhead costs for each production department. All these costs can be used as the basis for identifying the production cost of each product.
Practical Reasons for Using Absorption Costing
There are 3 primary reasons for using the absorption costing as follow:
- Inventory valuations: There are two main reasons that the inventory in hand must be valued. This first reason is to see the closing inventory figures to present in the statement of financial position. The second reason is to see the cost of sales presented in the income statement.
- Pricing decision: Basically, before setting the selling price, a business should look at all associated costs related to the product, including the overhead cost. Thus, using absorption costing would allow the company to allocate the overhead costs to the product to see the full cost of the product. The company may decide to adopt the full cost-plus pricing to set some desired profit during the pricing decision.
- Establishing profitability of different products: Similar to the pricing decision, when a business knows how much costs are incurred for each product, they can establish the profitability of each product by using relevant pricing decisions.
Advantages of Absorption Costing
- This method charges fixed and variable overhead costs in the inventory of the product units, which complies with GAAP rules.
- When costs are apportioned to different departments, it allows for the reallocation and reapportioning of the costs.
- If inventory levels are increased the profits tend to rise too, because of the practice of fixed overheads carrying to the next accounting period (in the income statement).
- The fixed costs are the same for any number of units produced, so accounting for the variable costs (both fixed and variable) is a more realistic approach in cost per unit calculations.
Disadvantages of Absorption Costing
- The absorption costing tends to give higher profits over a certain period of production because the closing inventory is accounted for in full, but over the longer period, the total profit will be the same as in any other costing method.
- Allocation, apportioning, and absorption of fixed and variables costs are difficult tasks for small businesses to perform.
- In the apportioning step of the method, there may arise a conflict in different departments, for example, the after sale department does not incur the production costs.
- The information provided using the absorption costing method sometimes can be insufficient for strategic decision i.e. in the long term.
Conclusion
The absorption costing method practices in line with Generally Accepted Accounting Practices GAAP, it also accounts for the full overhead costs. However to apply this method successfully the organizations need to consider caution while apportioning the costs, charging the inventory, and calculating the cost per unit. Once the production volume is decreased the overhead costs will be charged to a lower number of units which may result in lower profits.