Introduction
Marginal costing is another product costing which is very important for pricing strategy. In an imaginary world suppose you buy a piece of land, machines, set up a factory, hire skilled labor, and start manufacturing products. In one month’s time, you manufacture 5,000 items. The costs incurred to set up the manufacturing facility remain are 0.5 Million $. What would you do to recover those costs and make profits? Increase the volume of production, by how much? The marginal costing is an economics concept that deals with fixed costs over a period of production. It considers the change in the variable costs with the increase or decrease in the number of units produced.
Definition of Marginal Costing
Marginal Costing method is “An accounting system in which fixed costs attributable to the relevant production period are written off in full against the contribution, and the variable costs are charged to cost units.”
Read the definition again, it says the fixed costs are written off against the contribution, not waived off. This theory argues that the fixed costs would remain the same over the period of production, so the basis for management decisions should be based on the “contribution margin”. The variable costs will vary with the production, so an optimum level of production is found using this technique to find the break- even volume production. The contribution margin then becomes the basis for the calculation for:
- Break-even sales point
- Target profit margin
- Safety margin of profit
Contribution Margin = sales price per unit – variable cost per unit
Break-Even cost per unit = fixed cost per unit + contribution per unit
Target profit margin per unit = (fixed costs + profit) ÷ Contribution per unit

In other word, we can simplify as follow:
Total Profit = Total Contribution – fixed overheads
The idea of Contribution is slightly different from that of profit, where profit is simply an aggregation of the number of units sold. Marginal costing provides management with information on how much “contribution money” is there in the product mix.
Simple working example:
Suppose a factory produces stationery items like ballpoint pens. It produces 1000 units in one month.
The fixed overhead costs for the factory = 10,000 $ Raw Material (variable) cost = 2 $ per unit.
Units produced in one month = 1000 units
Fixed costs per unit = 10000 ÷ 1000 = 10 $ per unit. Total Cost per unit = 10 + 2 = 12 $ per unit.
If the management sets the price at 15 $;
The profit margin = 15 – 12 = 3 $ per unit.
But the price of 15 $ could be too high or too low in comparison to the competitors in the market. So if the factory doubles its production (2000 units in one month).
Variable per unit = 2 $
New fixed cost per unit= 10000 ÷ 2000 = 5 $ New total cost = 5 + 2 = 7 $.
New profit margin per unit= 15 – 7 = 8 $ per unit.
The concept of marginal costing comes handy when there are several products. The management will focus on the “contribution” from each product and will find the optimum product mix to maximize the profits.
Marginal Costing and Absorption Costing
Both these techniques treat variable costs (overheads) and finished inventory in different ways. The profit margins in the short term will be different in both methods, but eventually will be the same over the longer period or on the completion of the project.
- The absorption costing accounts for the fixed overheads, which causes over/under apportioning of the costs which may result in fluctuation of profits, whereas in marginal costing these overheads are charged in full without apportioning so the profits will remain the same.
- The absorption costing method charges the ending inventory at the full cost of overheads, but the marginal costing method charges the ending inventory at the contribution margin cost rate, hence the profits calculated for a certain period will be different in both cases.
We can summarize the treatment of both methods in a table like:
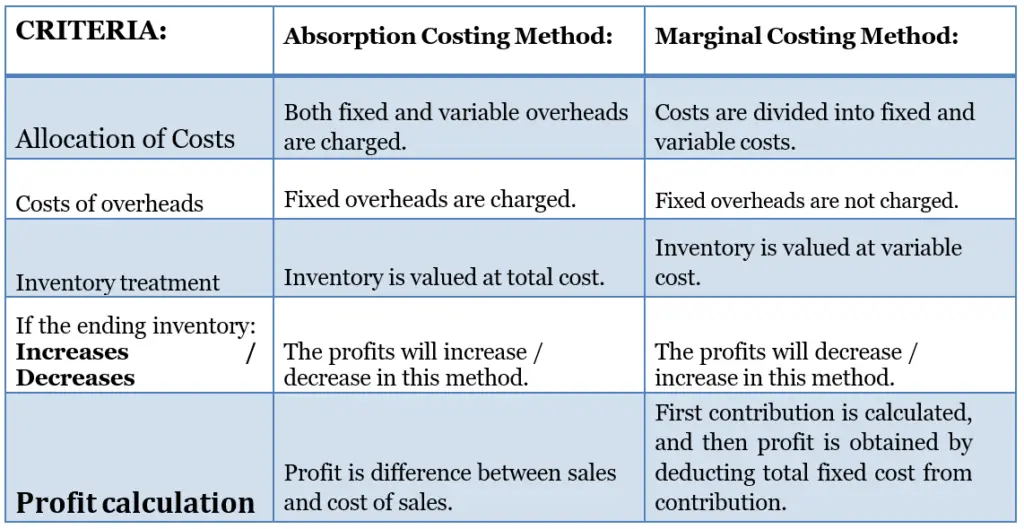
Conclusion
As we can see from the information above that both the costing methods provide different treatments for inventory costing and the calculation for the profits.
However, the profits calculated with both these methods over the long run will be the same. The only difference arises due to the treatment of ending inventory and the cost rate. Absorption costing calls for more careful analysis is difficult to implement and requires certain skills. The marginal costing on the other hand provides strategic management with straight forward information for the contribution margin and helps to obtain a certain product mix for profit maximization.