Introduction
In this article, we will cover the Direct Material Price Variance. As you know, variance analysis is one of the key performance management tools, where implemented controls are measured and revised. In any business, continuous improvement and quality management concepts cannot be achieved unless performance measurement is done regularly.
Definition
Typically, we commonly known variance as “The difference between the standard and the actual performance”
That is the simplest of the variance definition and can be applied to any variance techniques in price, cost, direct labor, etc.
The Direct material cost is often the largest part of the total cost in any manufacturing facility. Cost accountants are particularly keen about measuring direct material variance. Direct material price variance is part of the total material price variance. Total Material Price variance consists of two parts:
- Direct material price variance
- Direct Material usage variance
In this article, we will focus more on the direct material price variance while the direct material usage variance will be covered in another article
Important of Direct Material Price Variance Calculation
Direct material accounts for the largest portion of the product cost in manufacturing products so it affects the gross margins directly. As discussed above, it is also an integral part of the total material variance analysis.
- Direct Material Analysis helps production managers control material quality, prices, and wastes
- It can be performed before the full manufacturing cycle completion
- It helps the management identify and match the quality of raw materials from different suppliers
- Top management can use the analysis to decide on bulk purchase of inventory or to switch between the suppliers
- It helps top management to compare the “standard price” and “Standard Quantity” against the actual capabilities of the company
Direct Material Price Variance Formula
First, let’s see the formula for direct material total variance as follow and then we will break it down to both direct material price variance and direct material usage variance.
Direct Material Total Variance = (Actual Price – Standard Price) × Actual Quantity
For a detailed and comprehensive analysis, it is important to understand which elements can cause the variance, e.g. Actual quantity, standard price, or standard quantity.
To study the variance analysis in detail, following formula should be used:
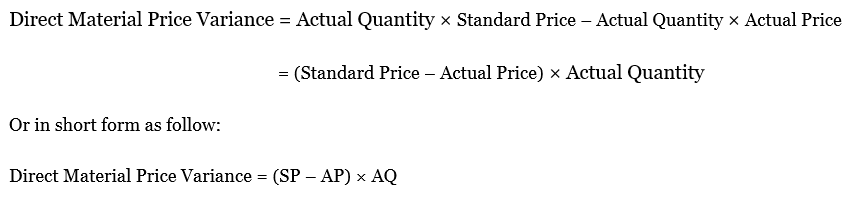
The total material variance analysis in detail can be appraised by studying both direct material price and Material Usage Variances. In this article, we’ll discuss the direct material price variance in detail.
Example Calculation of Direct Material Price Variance
Example 1:
Suppose Techno Blue manufactures a single product with following standard price:
Material Price = $10 per kg, Material Usage= 2 kg per unit.
Actual Performance:
Produced units = 1000 Material Cost = $20,900 Material used= 2,200 kg
Required: Calculate the direct material price variance.
Solution:
Using the simple formula above for direct material price variance, the calculation will be as follow:
Where the below information were given:
Standard Price (SP) = (10×2×1,000) = $20,000 or $10 per kg or $20 per unit
Actual Price (AP) = $20,900 [Per unit =$20.9 (20,900 ÷ 1000) or per kg = $9.5 (20,900 ÷ 2,200)]
Actual Quantity (AQ) = = 2,200 kg [Per unit = 2.2 kg (2200 /1000)]
Thus, the direct material price variance = (10 – 9.5) × 2,200
= $1,100 FAVORABLE
Example 2:
Continuing from example 1;
Let’s assume further that the total direct material cost is only $19,900 instead of $20,900. The other items remain unchanged.
Required: Re-calculate the variance.
Solution:
When the material cost is at $22,900, then the actual price per kg would be $9.04 (19,900÷ 2,200).
Thus; the direct material price variance = (10 – 10.40) ×2,200
= $880 ADVERSE OR UNFAVORABLE
Example 3:
Continuing further from example 1 above, let’s assume that everything remains unchanged; however, there is change in material usage. In this example, we assume further that the material price per kg remains unchanged at $9.5. The actual material usage to produce 1,000 units is 2,050 kg instead of 2,200 kg.
Required: Re-calculate the variance.
Solution:
If the usage of materials changes from 2,200 kg to 2,050 kg and the price per kg remains unchanged, thus the direct material price variance would be as follow:
Direct material price variance = (10 – 9.50) × 2,050
= $1,025 FAVORABLE
Explanation and Analysis of Direct Material Price Variance
As we can see a fraction of the deviation from the standards set by the company can cost a large amount of profit in total daily or monthly production. In contrast, while the costs of the materials increase to $22,900, the direct material price variance becomes adverse.
Additionally, we had another scenario where we changed the material usage to 2,050 kg to produce the same 1,000 units of the product. In addition, in this scenario, we assume the market price per kg remains unchanged. The purpose of these changes is to see if the efficient use of materials changes impact the direct material price variance or not.
As a result, the efficiency of using direct material may change the level of variance; however, it cannot bring the variance to adverse or unfavorable variance.
Therefore, adverse variance can only happen when there is changes in market price of the materials.
Often manufacturing managers set a higher standard material price and standard quantity to achieve favorable variance. Performing the analysis of variances of both material price and usage separately can help top management identify the lapses in the calculation of the standards. The Variance analyses are the key starting points for any top management deciding on annual or quarterly budgets. Any firm aiming for total quality management controls and improved efficiencies must carry out the direct material variance analysis, as it improves the set standards. Top management plans for the company in strategic terms, the operational managers then implement those plans. For a manufacturing facility, efficiency in operations, direct material costs, elimination of wastes, and continuous improvements are key points to success. Adverse or unfavorable variance can be caused due to several reasons.
Reasons for Adverse Direct Material Price Variance
Below are the various reasons that cause the adverse:
- Expensive raw material purchases
- Switching between the suppliers
- Inexperienced or incompetent management
- Wrong forecast data for standard price and quantity setting
- Lack of historical data to analyze the correct standard price and quantity
Reasons for Favorable Direct Material Price Variance
In more efficient and experienced manufacturing facilities the favorable variance can be achieved with:
- Selecting the right suppliers with long-term contract discounts
- Deciding precisely between storing inventory or using the JIT techniques
- Analyzing past available data to correctly and realistically set the standard price and quantity
- Revising the standards set regularly to match the actual performance
- Continuous process improvements to achieve operational efficiencies
Who is Responsible for Direct Materials Price Variance?
As the purchases of the materials are often associated with purchase managers and operational management, so improving on direct material price variance also becomes a liability of the production department manager. However, as we can see with the variance breakdown analysis, the total material variance consists of two elements price and usage. Where a purchase manager is responsible for direct material “price” the operational manager is responsible for the “usage”.
Therefore a combination of roles who are responsible for the explanation of such variance analysis. Below are several roles of management in managing the variance:
- Clearly the purchase manager is responsible for the quality and cheap price direct materials without compromising on the quality
- As the variance will change with the standard price and quality, so the cost accountants need to set the standards realistically
- Operational managers need to make sure the set standards meet the quality and waste is minimum that can improve on the usage variance and also improved relationships with suppliers to achieve bulk purchase discounts
- The top management uses variance analysis in budgeting and planning, hence they need to look into both components of the price variance analysis
Vaguely speaking the such analysis looks to be the responsibility of a purchase manager only, but if we analyze it in details different components affect such variance. The top management, cost accounting, and budgeting team need to work in liaison with the procurement team to make sure the best results are achieved.
Limitation of Direct Material Price Variance Analysis
Analysis of this variance analysis provides certain benefits, but there are few fringes attached to it also:
- The analysis cannot provide sufficient information of total material price variance as it is closely linked with usage variance also
- Operational managers often manipulate the standard price and quantity set to achieve a favorable variance
- It lures purchase managers to buy cheap and low-quality raw material to improve their variance results
- Matching the set standards’ price and quantity becomes difficult as the standards are set at the annual budgeting and planning time often once a year
- It should be read in conjunction with material usage variance as these interlinked, e.g. zero wastes improve material usage and total variance becomes favorable
Conclusion
For improvements in budgeting, planning and controls; Variance is as important a tool as forecasting. For manufacturing process improvements, waste elimination, and total quality management the direct material price variance can provide valuable analyses. We should implement such variance analysis as a total management approach to achieve the best results rather than a purchase price metric. Collaboration between procurement and operational managers can yield favorable variance, as well as can help top management improve with the strategic planning with budgeting and control measures.