In factories, industries, and big corporations the accurate estimation of production cost is a significant chapter. Large quantities of homogenous objects are often being produced in the industrial sector on regular basis. During the manufacturing process evaluation of direct and indirect costs is an important segment. To efficiently calculate the cost of the total production process costing system is utilized by the manufacturing departments.
Table of contents
- Definition
- Features of Process Costing
- When should a Business Use Process Costing?
- Calculation of Cost per Unit in the Process Costing
- Framework Dealing with Process Costing – Step by Step Approach
- Types of Loss in the Processing Costing
- Example and Calculation
- Types of Process Costing in Valuing Inventory or Work in Progress
- Conclusion
Definition
Process costing also known as “Continuous Costing” is the concept of cost accounting which refers to the collection and allocation of manufacturing costs to the number of units produced. The companies or manufacturers estimate how much goods are produced and how much expense is incurred to produce the product.
In mass production when there is an order of manufacturing identical units the processing cost system is preferred by companies to track overall costs and overall inventory being produced.
Let’s consider a firm manufactures a huge quantity of similar products. Each process goes through separate departments. In July direct material cost is $150,000 and the conversion cost is $225,000. If the equivalent cost is prepared in July then each unit cost will be $2.25 for conversion and $1.15 for direct materials. Then the cost will be transferred to the next department in which processing cost would be added.
Features of Process Costing
- It is an ongoing process in which production of the stock is continuous, excluding the case when the plant is close down for maintenance, until the final product.
- The out result of the first process turn as raw material for the second process and this method goes on.
- In cost processing, to get the final product two or more processes are performed.
- During each process, the cost is accumulated. The complete cost of every process is divided by the out return of that process to calculate per unit cost.
- It is possible to bear normal and abnormal wastage due to avoidable & unavoidable reasons in the whole manufacturing stages.
- The final output of all processes may be the solo product but can be joint or by-products. When all products have the same importance and worth then it is called a joint product. Whereas, if one product has more worth and importance than others then it is known as a by-product.
- By-products required additional process before selling them while the main product does not need additional processing. A final product of one industry may be considered as a by-product of another industry.
- Through the cost of equivalent products, the work in progress is transformed into the final product.
When should a Business Use Process Costing?
Process costing is suitable for firms that produce constant wholesale units by a series of processes or operations. The companies estimate the cost of material, labor, and overheads. This cost ascertainment method is widely used by sugar, oil, steel, soap, paint, and chemical, etc. mass production industries. A set of similar operations are performed in each unit of manufacturing. Therefore, in each unit equal cost of overheads, labor and material is charged.
Calculation of Cost per Unit in the Process Costing
There are four major steps included in the calculation of process costing;
- Collect Direct Spending: At the account or sub-account level gather the pool of direct expenditures. This pool comprises of energy, depreciation, labor, and ledger information a company plans to spend.
- Allocate Indirect Spending: Next step estimates the costs that occur outside the manufacturing location such as drivers.
- Compute Cost Center Rate: Calculate the dollars per batch, per machine hour, or unit production rate.
- Proper Allocation of Process Rates to Products: In the last step you can allocate cost to the production units. Through the estimation of process cost, companies know how much charges arise as products go by manufacturing stages.
Framework Dealing with Process Costing – Step by Step Approach
The basic concept of process costing is clear let’s move on to how it works. Below is the chart showing the four key steps of process cost.
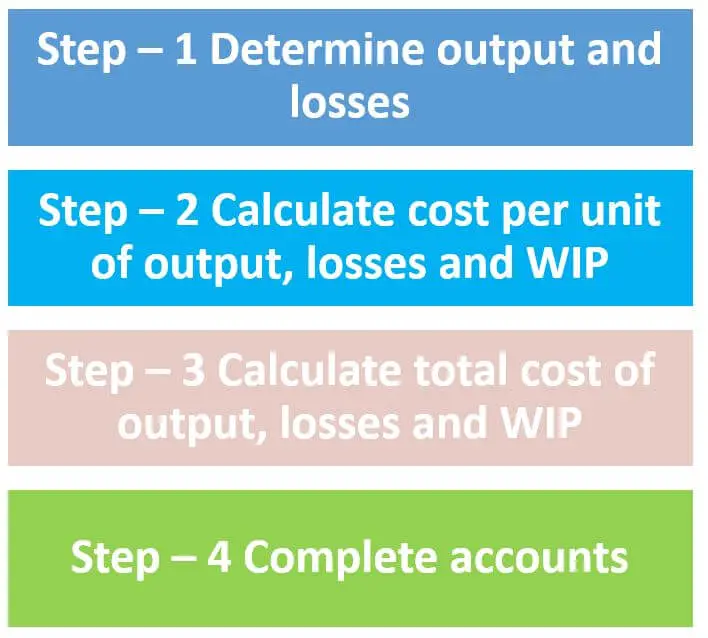
Step 1: Determining output and losses
In this step, it involves the following:
- Determining the expected output
- Calculating the normal losses, abnormal losses and abnormal gains
- Calculating the equivalent units if there are any opening or closing of work in progress (WIP). The equivalent unit refers to the completed number of units during a certain production stage. To calculate the total number of work in process units are multiplied with units that are completed.
Step 2: Calculating cost per unit of output, losses and WIP
In this step, it involves the calculation of cost per unit or equivalent cost per unit. To get the total cost all the costs are added together and then it is divided by a complete equivalent unit number to estimate the average equivalent per unit cost.
Step 3: Calculating total cost of output, losses and WIP
In this step, it involves the calculation of total cost, losses and WIP of the process costing. Typically, if there is any opening or closing of WIP, we will have to prepare the statement of evaluation.
By adding a cost to work in process and equivalent unit the company can make sure they are leaving unturned costs.
Step 4: Completing accounts.
In this last step, it involves the completion of the process accounts.
Types of Loss in the Processing Costing
In this costing two types of losses are identifies;
- Normal Loss: In manufacturing, it is the unavoidable loss of units that happens because the nature of raw materials is being processed.
- Abnormal Loss: It is the spoilage of units that should not happen during efficient or normal working situations.
- Abnormal Gain: It is the gain when the actual loss is less than the normal or expected loss. This will result in a negative cost.
Example and Calculation
Let’s assume that the total level of output is 2,000 units is required in the process costing of producing the final output of computer. 3,000 units of materials are put into the process. Below are the process costs that involve in the production:
- Materials: $10,500
- Conversion costs: $5,800
Normal loss is usually at 15% of input.
Prepare a process cost accounts together with the appropriate abnormal loss/gain.
Solution
In order to prepare a process cost accounts, we will illustrate the four key steps as we covered in the above section.
Step 1: Determining output and losses
From the example above, we have the total output of 2,000 units. Thus, we can calculate the losses as follow:
Normal loss = 15% × 3,000 = 450 units
Abnormal loss = (3,000 – 450) – 2,000 = 550 units
Step 2: Calculating cost per unit of output and losses
Cost per unit = Cost incurred/Expected output
The cost incurred here refers to the materials and conversion cost which is totally $16,300 (10,500 + 5,800). While the expected output is the addition between the required output and the abnormal losses which is 2,550 units (2,000 + 550).
Therefore, we can calculate the cost per unit as follow:
Cost per Unit = 16,300/2,550 = $6.39
Step 3: Calculating the total cost of output and losses
$ | |
Output (2,000 × $6.39) | 12,780 |
Normal loss | 0 |
Abnormal loss (550 × 6.39) | 3,515 |
Total | 16,295 |
Step 4: Competing process accounts
PROCESS ACCOUNT | |||||
Unit | $ | Unit | $ | ||
Material | 3,000 | 10,500 | Output | 2,000 | 12,780 |
Conversion costs | 5,800 | Normal loss | 450 | 0 | |
Abnormal loss | 550 | 3,515 | |||
Total | 3,000 | 16,300 | 3,000 | 16,295 | |
ABNORMAL LOSS ACOUNT | |||||
$ | $ | ||||
Process a/c | 3,515 | Income Statement | 3,515 |
Types of Process Costing in Valuing Inventory or Work in Progress
Weighted Average Cost: It is calculated the cost of goods available for selling divided by no. of units available for sale
Standard Cost: It is planned or budged cost in which the comparison of the expected cost is done with actual cost and the difference is charged by variance account.
First in First out (FIFO): Complex method that occurs when there are changes between layers of costs and production periods.
Which Method Should be Used?
All three types of this costing are essential. The use of methods depends on the production requirements of the firm.
Conclusion
Process costing is a standardized process with a continuous flow. It is a beneficial method to identify the cost of large batch production